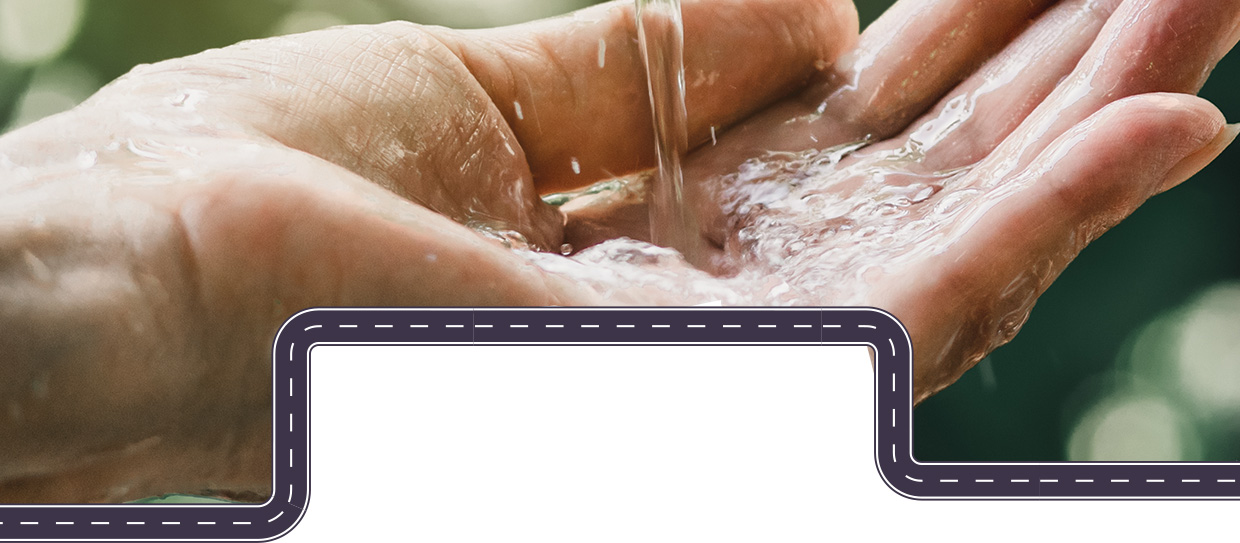
Our ambition is that, by 2030, our breweries will be carbon neutral, the packaging we use will be recyclable, the ingredients we rely on will come from sustainable sources, and we shall continue to be the best in industry in terms of water consumption.
As per Asahi Group’s policies, all environmental-related matters are dealt with by an environmental management committee led by Technical Vice-President. The Committee advances the activities in line with the Plan-Do-Check-Act (PDCA cycle and runs environmental management programs in full compliance with ISO14001 and ISO50001 and other regulations, as well as those included within the environmental permits for each location. All our sites operate based on ongoing plans aimed at increasing the processes efficiency and loss elimination. The ultimate goal is to achieve the environmental goals by 2050.
WATER MANAGEMENT
Water is one of the most important natural resources, essential for survival, and risks to water quality and quantity are increasing. According to the European Environment Agency's (EEA) 2020 report, only 40% of Europe's surface waters have good or high ecological potential.
Moreover, extreme water-related events, such as floods or droughts, have become increasingly frequent, with a significant impact on people's economy, health and well-being.
The EU has developed a number of directives and policies to address water issues, including the Water Framework Directive, the Drinking Water Directive and the Industrial Effluent Directive. It is important to protect water resources and the environment to ensure that we can continue to use them sustainably and leave them in good condition for future generations.
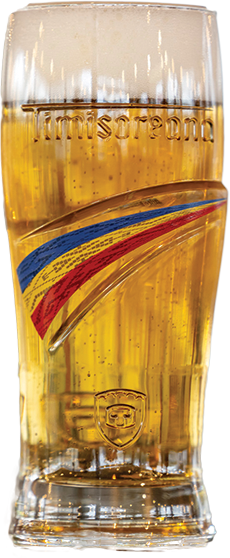
The EU has developed a number of directives and policies to address water issues, including the Water Framework Directive, the Drinking Water Directive and the Industrial Effluent Directive. It is important to protect water resources and the environment to ensure that we can continue to use them sustainably and leave them in good condition for future generations.
For Ursus Breweries, water is among the most important ingredients in the brewing process, and excessive consumption can have a significant impact on the environment and communities. Fortunately, we had the advantage of operating in areas without water stress, so the impact is low. However, we continue to take proactive steps in our production processes to reduce water consumption and support resource conservation.
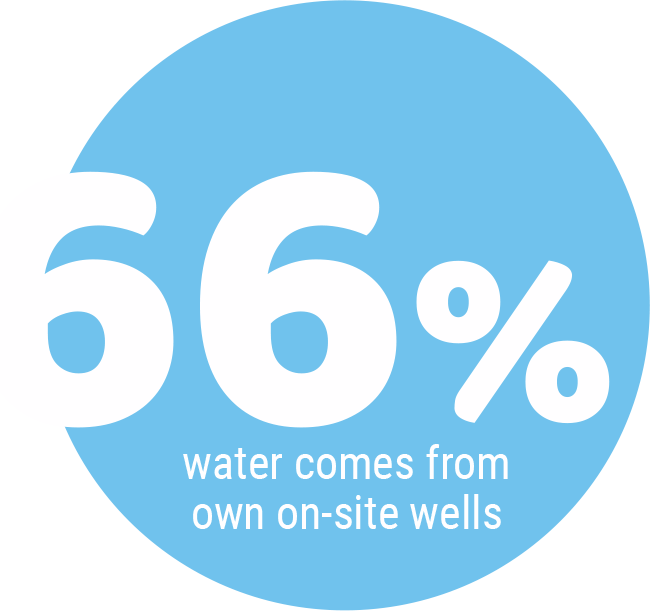
Approximately 66% of the water used in breweries in Buzău, Brașov and Timișoara comes from their own on-site wells and the rest from the municipal network. At the mini-brewery in Cluj-Napoca, water is supplied exclusively by the municipal network.
To ensure responsible use of water resources, each brewery has its own consumption targets.
In order to track and meet targets, water use performance is monitored on a monthly basis to achieve continuous improvement. Water volumes are measured using flow meters installed in each plant. In addition, measurements are also carried out on specific areas within the breweries.
By 2025, our target is to lower the average consumption to 2,75 liters of water per liter of packed beer.
We comply with environmental protection legislation and regulations, and our environmental management procedures also follow voluntary standards that impose more stringent requirements than those required by law. These apply to the entire water management system, from water supply to wastewater processing.
Water quality can influence the quality of our products, which is why we use our own water treatment plants before the water enters the internal circuit to ensure that it is properly purified and meets our high-quality standards.
As for effluents, they are treated in our wastewater treatment plants, according to environmental permits, before being discharged into municipal sewage systems. Following effluent treatment, we obtain biogas which is then used in some of our production processes to reduce gas consumption.
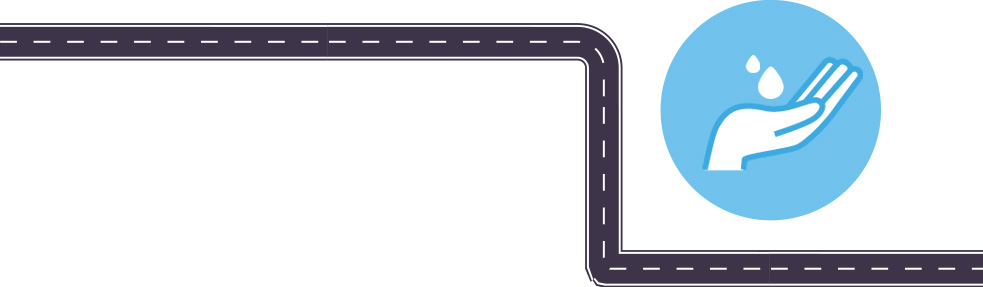
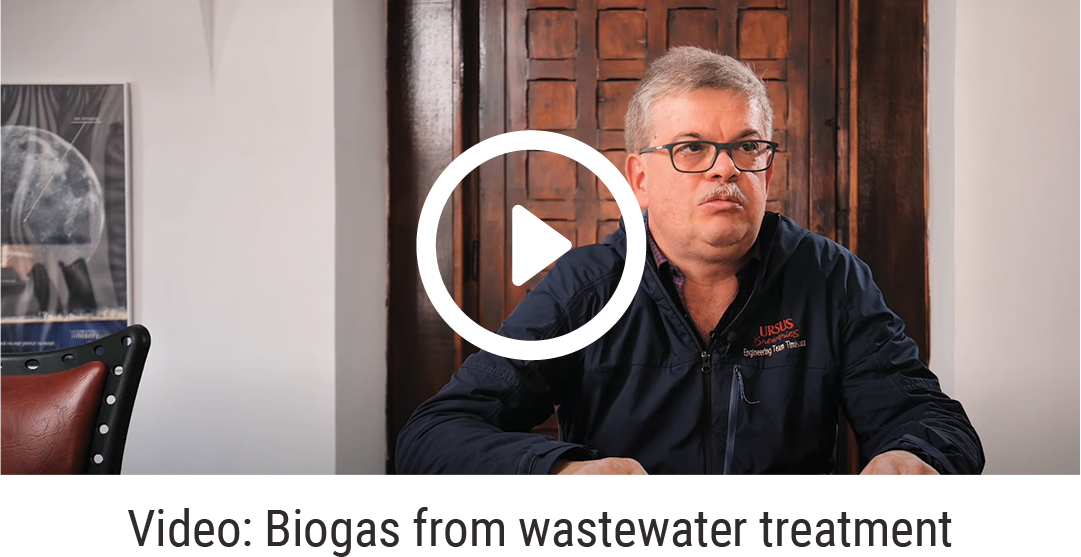
To make water consumption more efficient, in the reporting period, we continuously monitored consumption, compared optimal consumption, applied a Kaizen approach to manage water losses and streamlined processes to achieve our targets. In addition, we have promoted a water-saving culture among employees and we have reused/recirculated water in various production processes. Following the consumption assessment processes, we continue our improvement and operational efficiency processes, ensuring the same high level of quality of our processes and products.
Throughout the reporting period there were no complaints from the community or sanctions related to water management. To contribute to the responsible use of water resources, we are planning a water risk audit in Ursus Breweries in 2023.
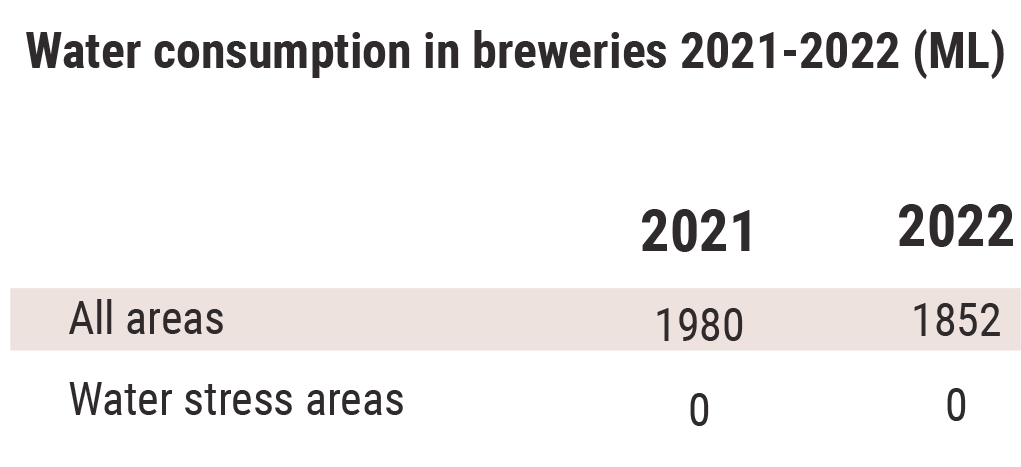
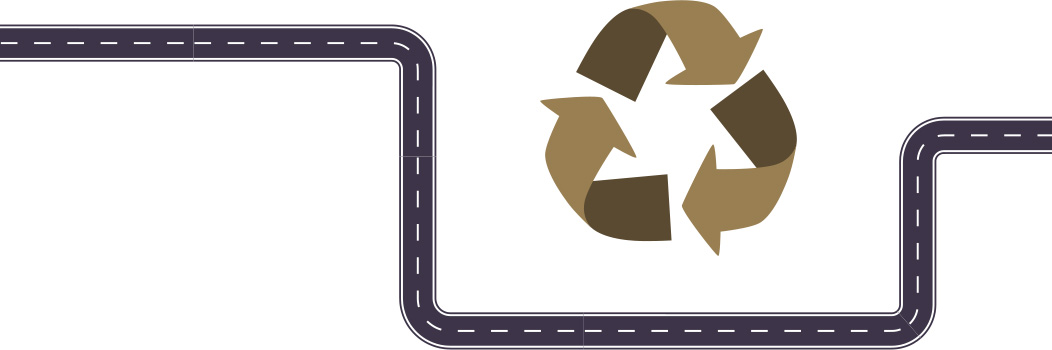
CIRCULAR ECONOMY & PACKAGING
In order to promote recycling and waste reduction, EU Directive 2018/852 on waste management and recycling has been transposed into Romanian law. Thus, specific rules and obligations on packaging waste management have been established, including the introduction of a system of selective waste collection and recycling of packaging waste, involving the extended responsibility of packaging producers and suppliers.
Also, Law 211/2011 on the waste regime continued to be the main legislative framework for waste management in Romania. Moreover, the National Circular Economy Strategy was adopted in 2022 to support the country's transition to a circular economy model. Together with an action plan, they will contribute to achieving the overall objectives of the European Green Pact and the objectives of the EU Circular Economy Action Plan.
The importance of this topic is given by numerous regulations and our strong interest in managing these issues is directly reflected in the company's actions. It is important that the packaging provides consumers with the desired quality of our product and that it is as environmentally friendly as possible. Thus, we focus on the life cycle of beer packaging and the efficient use of resources used in its production.
During 2021-2022 we have succeeded in reducing the amount of materials used in packaging and continue to focus on promoting the use of reusable packaging.
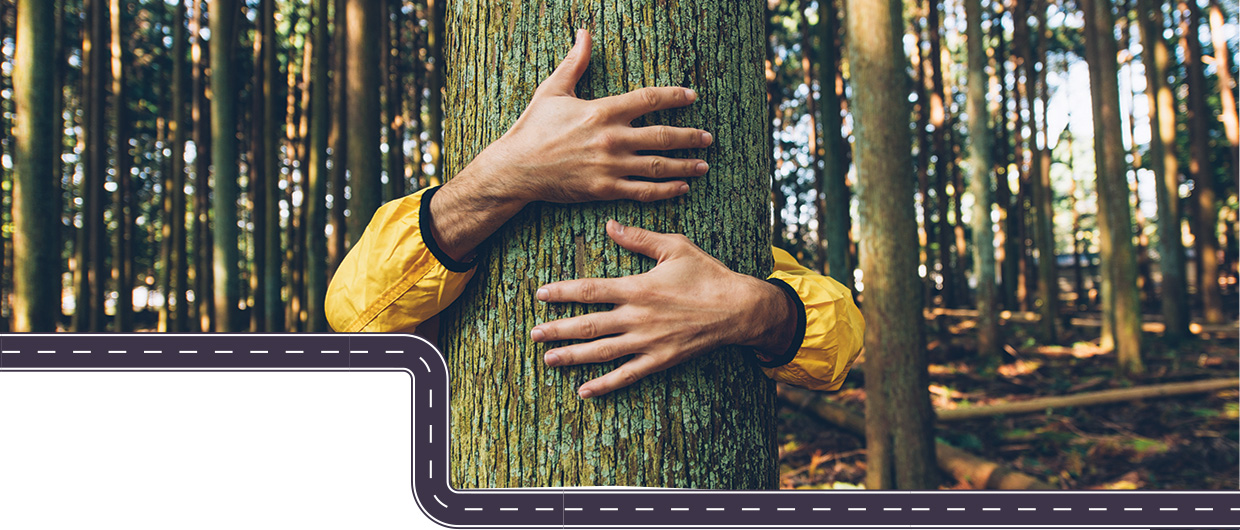
One of our specific targets is to reduce plastic used for packaging by 25% until 2030 compared to the baseline year 2019.
In the last two years, we carried out actions to reduce the amount of raw materials used, particularly as for the glass and plastic used. Some examples of initiatives are: reducing the weight of PET or glass primary packaging and weight of plastic lids, changing the specification of shrink films and stretch foils or using other solutions to replace them at certain stages of packaging (e.g. adhesive).
We also discontinued PET packaging for the URSUS brand in 2021 and removed paper labels from the neck of PET packaging.
Such actions brought a reduction of plastic use by approx. 24% compared to the reference year.
Beyond actions to reduce the materials used for packaging, we also focus on the use of recycled content materials. Thus, during 2022, we were able to switch to 50% recycled content for shrink foils for certain packaging (up from 0% in 2021), and our six packs and carton trays for cans are now made of 100% recycled material. Around 66% recycled material is used for the glass bottles.
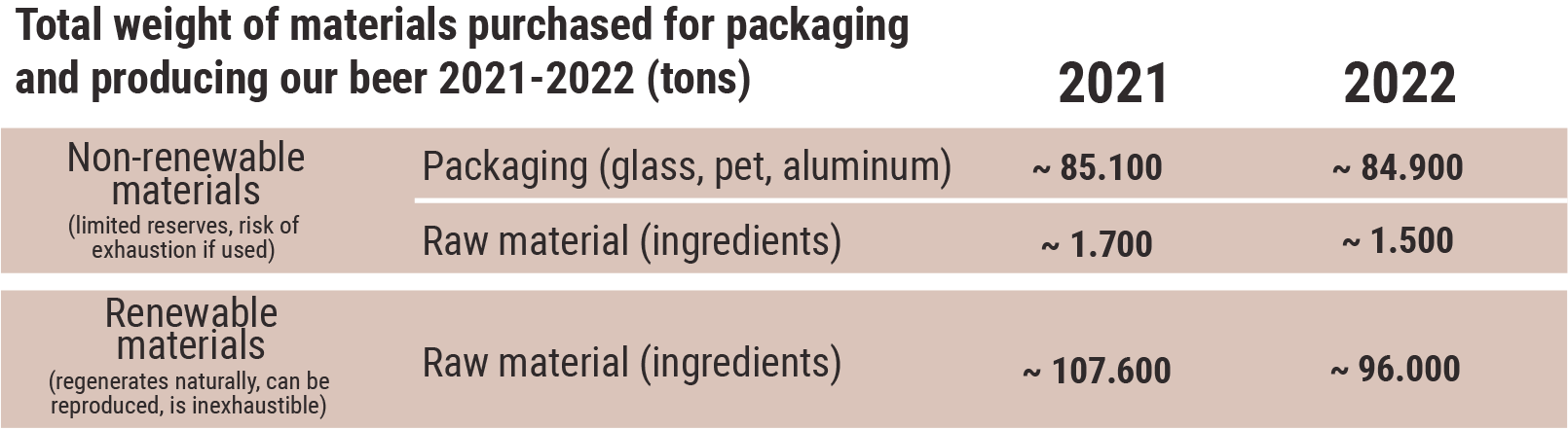
WASTE MANAGEMENT
We continued to fulfil our responsibilities for the recovery of packaging/ packaging waste generated from the consumption of products placed on the national market through organizations implementing extended producer responsibility obligations. Thus, the annual legal targets have been fully met by recycling of packaging waste, recovery or incineration in energy recovery incineration plants.
In order to promote a circular economy, we informed and encouraged consumers to collect waste selectively, either during the big festivals we attended (UNTOLD, Neversea, Oktoberfest) or through dedicated campaigns such as ‘Keep nature clean’ in Ciucaș Relaxation Areas.
Details of these can be found in the Responsibility chapter, Investments in community and local partnerships section.
Together with the other members of Brewers of Romania Associations and Romanian Soft Drinks Association members, reunited in the Beverages Producers Alliance Romania, we continued to contribute to the implementation of Deposit Return System in Romania.
The system will complement existing efforts in packaging waste management and support the achievement of the collection and recycling targets set at European level by the European Union's circular economy strategy.
The launch of the national Deposit-Return system in Romania is planned for November 2023.
In 2022, the RetuRO company operating the system obtained the license to operate and started the procedure of organization and construction.
Waste from our production activities is monitored and reported according to regulatory requirements by executive managers following the monthly technical report format developed by Asahi. The reported waste comes from the brewery activities in Brașov, Buzău and Timișoara and is monitored in order to reduce the amount of waste per hectoliter of beer produced.
By 2025, Ursus Breweries' target is to reduce the amount of production waste sent to landfill to zero.
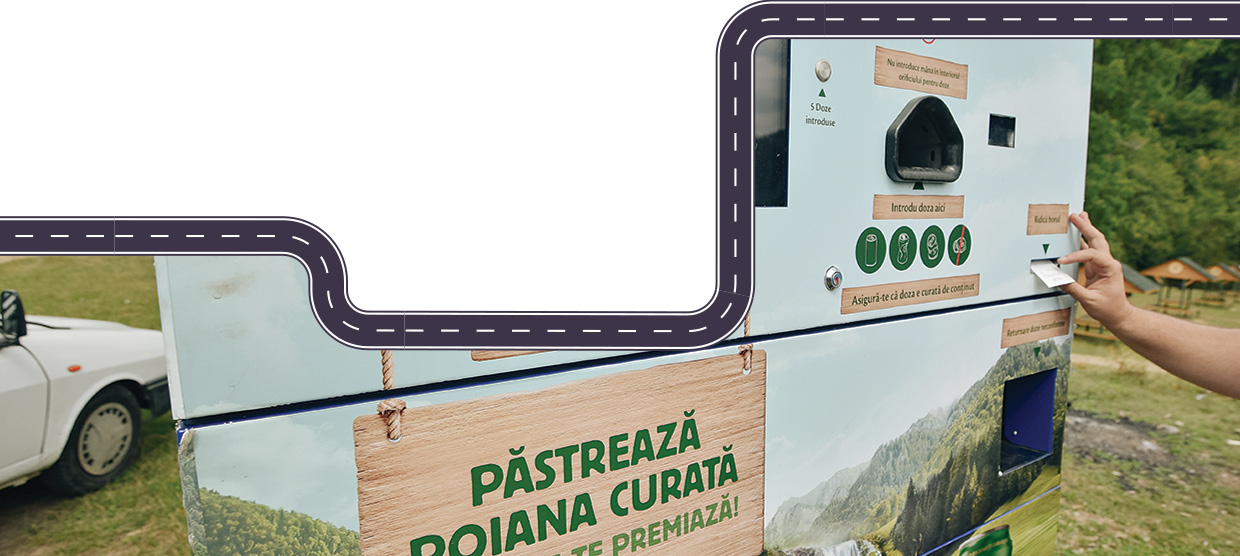
In 2022, a best practice example is the factory in Brașov, where we have achieved the performance that 90% of the waste to be recycled, thanks to the reuse of two types of residues in agriculture, resulting from the treatment and filtration processes. Glass, wood, cardboard and plastic waste are collected separately and sent for recycling.
Waste generated within Ursus Breweries: Buzău, Brașov, Timișoara and Cluj-Napoca are related to beer production and are regulated within the Environmental Permit for each site: Integrated Pollution Prevention and Control Directive 96/61/CE (IPPC) permit for Buzău, Brașov and Timișoara and simple permit for Cluj Napoca. The specific types of waste the breweries are disposing are managed by third parties authorized for waste management by Romanian regulatory.
We strive to increase the amount of waste recycled every year. To achieve this, we follow plans to prevent and reduce the amount of waste generated. The plans were first developed in 2022 based on an external audit and will be updated year by year.
These are available on www.ursus-breweries.ro/media/materiale/.
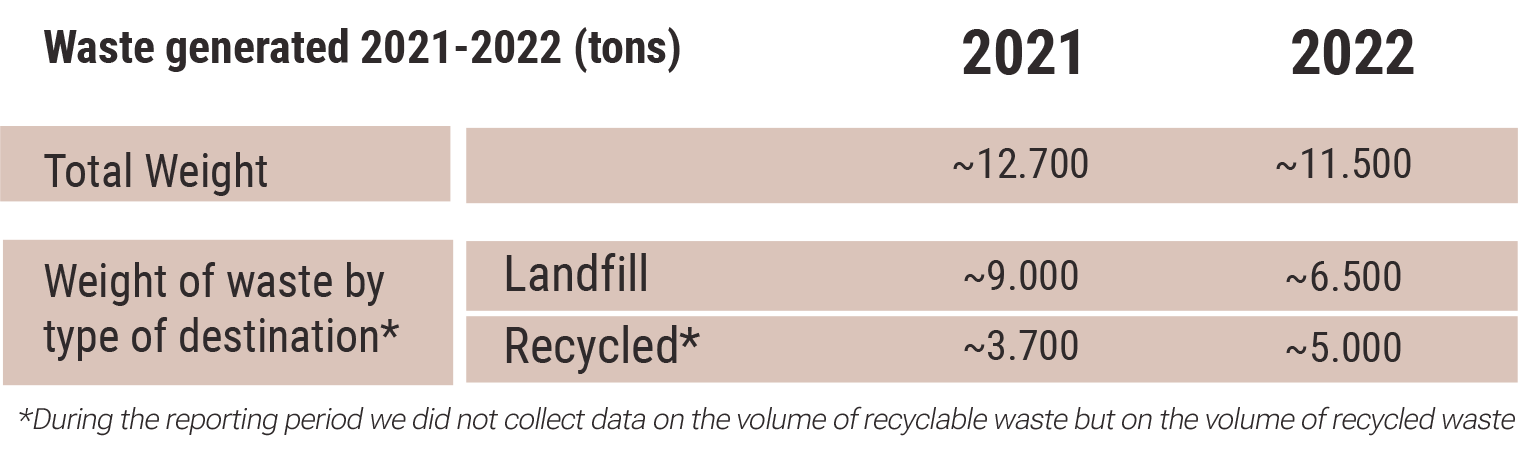
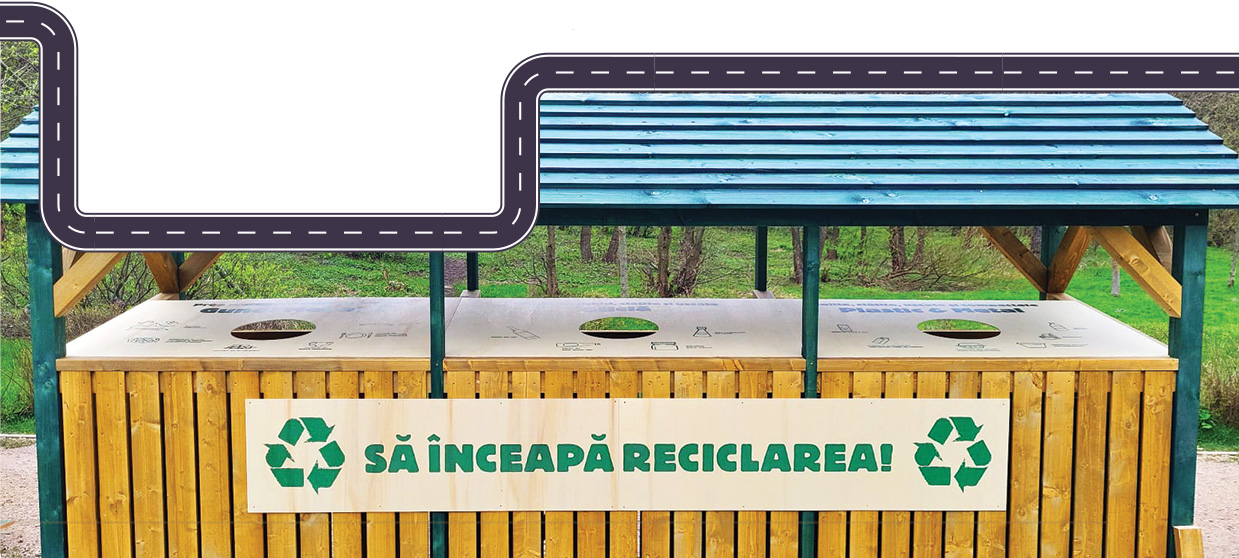
CARBON DIOXIDE EMISSIONS’ MANAGEMENT
There is an increased interest of the international community towards reducing CO2 emissions. The most significant ones are the UN’s call for action on climate, and the European Climate Law, that sets the framework for reducing net greenhouse gases and achieving climate neutrality.
Through the Paris Agreement, there is a global commitment to limit the average global temperature increase to 1,5 degrees Celsius, which is considered crucial to avoid serious consequences of climate change.
As the main contributor to global warming and climate change are carbon dioxide emissions, one of the main directions of Ursus Breweries' sustainability strategy is to reduce them so that the negative impact on people, the environment, the economy and including our business is minimized.
The importance of these issues, as well as the Asahi Group's view on environmental challenges, are described in detail in the 2022 report of the task force on climate-related financial disclosures (TCFD), available here.
The importance of these issues, as well as the Asahi Group's view on environmental challenges, are described in detail in the 2022 report of the task force on climate-related financial disclosures (TCFD), available here.
By 2030, we intend to become carbon neutral within our breweries
Moreover, we intend to actively engage suppliers and partners in reducing carbon dioxide emissions across the whole supply chain by 30% in the same period.
Our ultimate goal is to become carbon neutral across the supply chain by 2050.
A key commitment to achieving these goals is the one made by the Asahi Group by joining the global RE100 initiative to use only renewable energy for its operations. We are fully aware that the overall impact of our products is not just in breweries, this is why we aim at initiating partnerships and cooperating with our suppliers and customers to accelerate reductions of emissions, especially in the area of packaging, transport and cooling of beer.
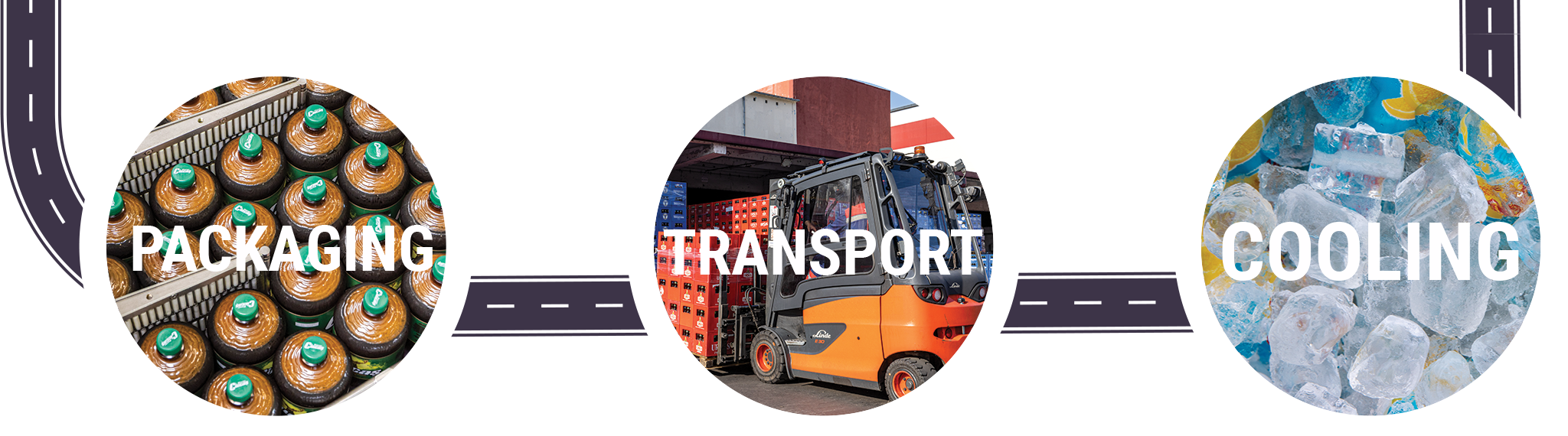
ENERGY CONSUMPTION
The operational control in place is focused on fossil fuel emissions reduction. Calculation of CO2 emissions resulted from the activity of Ursus breweries in Buzău, Brașov, Timișoara was performed based on Ursus Breweries energy and emissions reporting procedure. The value of the emission factors used for reporting of Scope 1 emissions related to Ursus Breweries were communicated by the National Environmental Protection Agency. The total electricity consumption within the three factories of Ursus Breweries was supplied via national grid, and the CO2 emissions for Scope 2 were calculated based on the emission factors provided by our electricity supplier.
To reduce energy consumption, both electrical and heat, each brewery has a plan to increase the efficiency of the production process based on the elimination of losses and uses the ISO 50001 energy management system. Also, the energy management aiming to reduce carbon emissions also takes place through actions, such as: installing equipment to reduce consumption (e.g. LED lighting), automating processes, replacing natural gas used for certain processes with biogas produced in the wastewater treatment plants, implementing heat recovery systems, replacing condensate recovery systems with improved versions in terms of performance, etc.
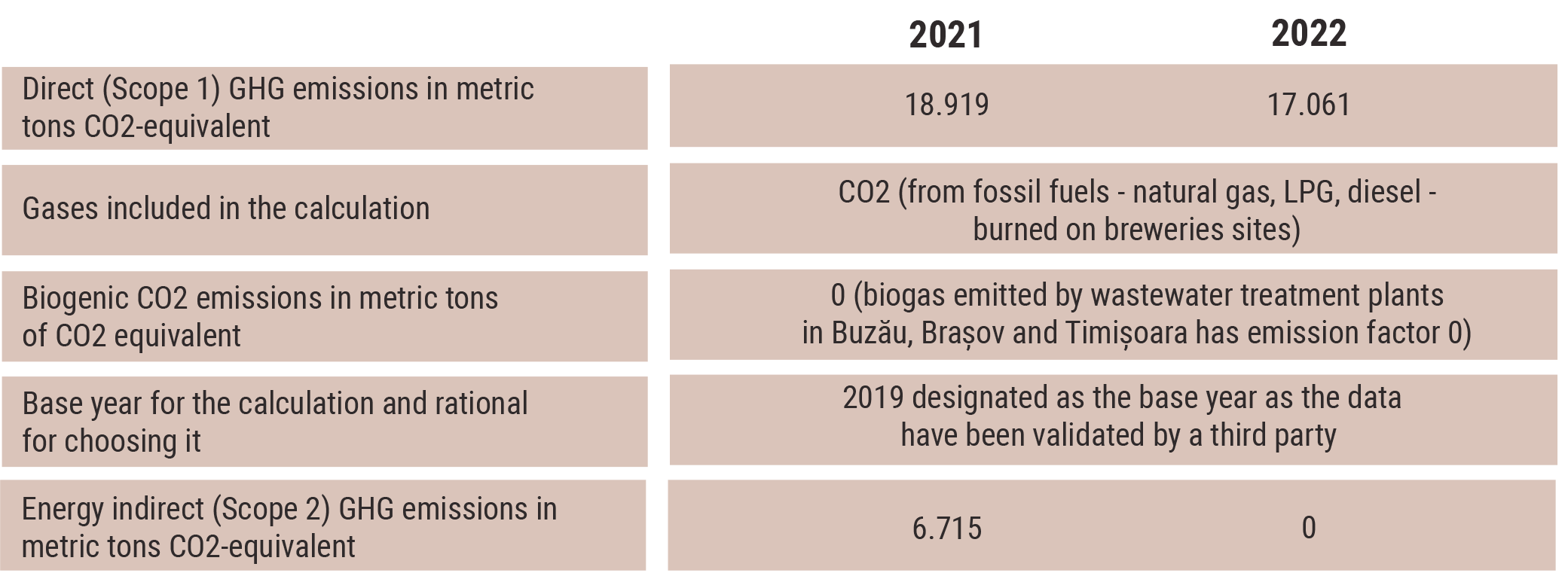
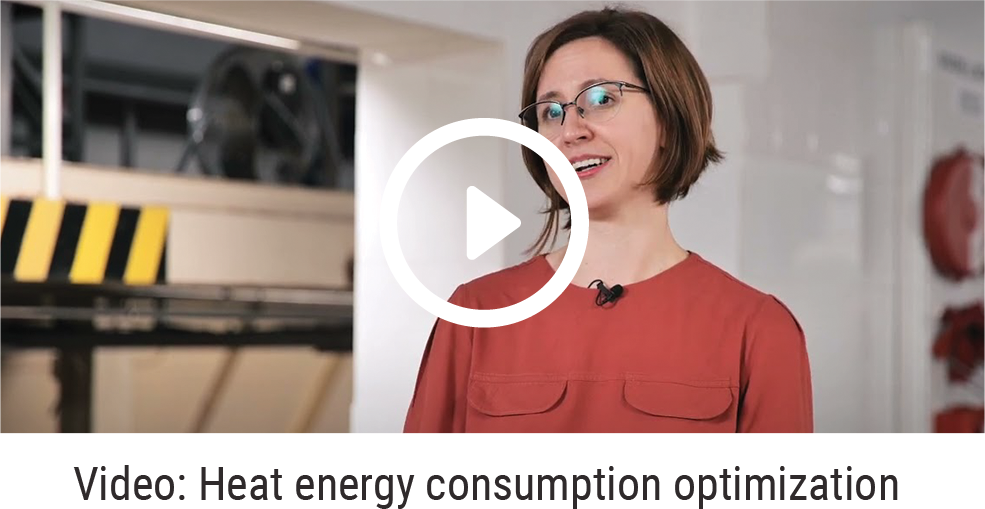

In 2022, another specific initiative was the replacement of the dye used for PET preforms with another one that allows faster energy absorption and, implicitly, the reduction of dioxide carbon emissions. To reduce carbon emissions, we also use fully electric forklifts, instead of LPG powered ones.
TRANSPORT
Currently, transport emissions represent about 25% of total EU greenhouse gas emissions. Due to the drastic drop in transport activity during the COVID-19 pandemic, emissions are estimated to have fallen by 13,6% between 2019 and 2020, then increased by 7,7%, in 2021, as the economy recovered.
Our products are transported from breweries to warehouses and from there to trade destinations. These routes are necessary and are a cause of our indirect emissions, an impact that must be taken into account. Currently, these activities are carried out by suppliers (transporters) using their own fleet or contracting independent transporters.
They are identified, selected and contracted by the procurement department, which is responsible for setting technical criteria and managing contracts. In addition, the national distribution team manages the entire transport activity: transferring products between breweries and warehouses, financial aspects, route optimization, truck loading and loading rate, and setting and monitoring key performance indicators. We take active steps to improve performance, based on the local action plan and performance indicators. The impact of our transport is directly influenced by the performance of the transport means available in the contractors' fleet.
The efforts we make through the distribution and purchasing teams are to optimize transport, reduce the number of kilometers travelled by optimizing the volume loaded and raising awareness among customers to issue orders that allow fewer truck trips to be used for the same volume of product. We are also working hard to increase the percentage of direct brewery loads and to reduce the short runs between the brewery and the warehouse, which were made to avoid a possible saturation of brewery space.
In 2022, thanks to a pilot transport project, we were able to deliver the same volumes to customers using up to 150 fewer trucks than in normal operation, reducing carbon dioxide emissions and achieving the best delivery performance in recent years.
On the other hand, we are directly responsible for the fleet of our own employees. Our marketing and sales team travels the country to promote products, attend events, work with retailers and customers and support them in their business efforts. To limit the negative impacts caused by transport, during 2021-2022, we have increased the share of gasoline cars to 68% from 1% in the old fleet in 2020 and purchased lower carbon vehicles. Old fleet cars now account for only 5% of the total and we will continue to replace them with more emission-efficient ones. During the same period, we bought 3 plug-in hybrid cars, which are 2,2l/100km more fuel efficient than other gasoline cars. Hybrid car purchases will continue in 2023.
Also, to reduce fuel consumption, the cars are equipped with a GPS module to better map the routes and optimize the reporting activity (kilometers driven, average consumption).

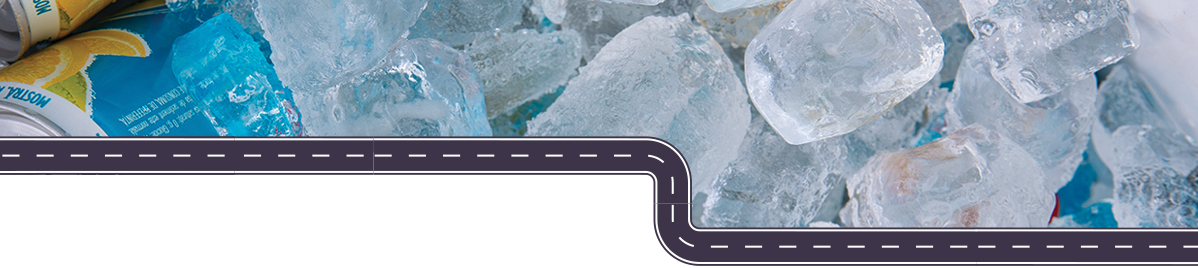
COOLING
Cooling is a key factor in maintaining the quality and freshness of our beers. The impact takes place in our warehouses and distribution channels (stores, HoReCa locations, events). It is not enough just to manage direct impact, we need to strengthen cooperation with business partners and support them in order to become aware of their own impact. Over 73% of the beer fridges and draught coolers (pint, glass) in locations where our beer is sold are owned by the company.
The equipment is offered free of charge, but operating costs (such as electricity) are borne by customers. Currently, we cannot collect valid energy consumption data, and estimating data based on cooled beer volume would be inaccurate. However, we have developed a commercial asset management policy with the aim of substantially reducing our environmental footprint by purchasing modern equipment that operates with modern cooling agents and is fitted with an operating control system (day/night, summer/winter) as well as LED lighting.
Our purchasing departments are proactive in choosing suppliers capable of delivering high tech coolers, and colleagues in operations and sales are working to replace those less energy-efficient.
As of 2021, our efforts have been directed towards purchasing class D energy efficiency index commercial fridges, gradually improving their performance to class A energy efficiency index by 2030 if technology becomes available.
We are ahead of schedule by purchasing, as early as 2021, refrigerators with EEI=C performance, not 100%, but only on models for which better performance was available for purchase (the performance scale for commercial refrigerators is different from the scale used for household equipment).
So far, we have inventoried the lower-performing units (E, F, G) and started the process of their phased replacement in 2021. In addition, all new locations are equipped with energy efficient cooling units as per the yearly chart below.
Between 2021 and 2022, more than 5.500 old refrigeration units with lower cooling efficiency technology have been removed from Ursus Breweries’ ownership. With the new purchases we managed to replace more than 4.800 coolers, some of which were still functional but energy inefficient. In doing so, we have also registered a loss of previous investments in order to increase the speed at which we decrease our carbon dioxide footprint.
In 2022, replacement plans were affected by the conflict situation in Ukraine as deliveries of coolers were delayed. However, by 2030, we continue to aim to have only the highest energy-efficient fridges available in the year of purchase.